Working POTA
Back at the beginning of the year (2024, that is) I volunteered to be Newsletter Editor for the local radio club (Nashoba Valley Amateur Radio Club – NVARC). I also started a monthly column in the newsletter – Working POTA in which I regale the crowds of my adventures in the field making radio contacts for Parks On The Air (POTA).
In the throes of excitement over becoming editor and writing a column, I voiced the intention of making 500 (yes, five hundred) radio contacts each month for the year 2024. I’ve managed to do four months. I still have about 200 to go for the month of May. Conditions have been horrid for much of the month, either from a weather perspective (I don’t like setting up in the rain) or from a space weather perspective (those Coronal Mass Ejections that make pretty Northern Lights ruin radio for a few days).
Yesterday (20 May 2024) I managed to get out on a nice day. I made 66 contacts from a little corner of the Oxbow NWR that intersects the Nashua River, so it counted as 132 POTA contacts. These “two-fers” are my salvation when time is tight and I have to make a lot of contacts.
I used a 20 meter delta loop antenna strung from a tree and staked out at the ends. The base was about 5 feet off the ground, and I’m guessing the apex was around 30 feet. The support was 10# monofilament fishing line. I staked it out with a couple of tent stakes and some orange paracord. The antenna itself is orange. If the pedestrians can’t figure this out, I’m sorry. I can’t make wire blink.
Coverage was pretty good into the Midwest, but I noted late in the activation that the antenna was not plumb, and the Europe-favoring broad side of the loop was pointing at a sub-zero takeoff angle (i.e. pointing below the horizon, not above it).
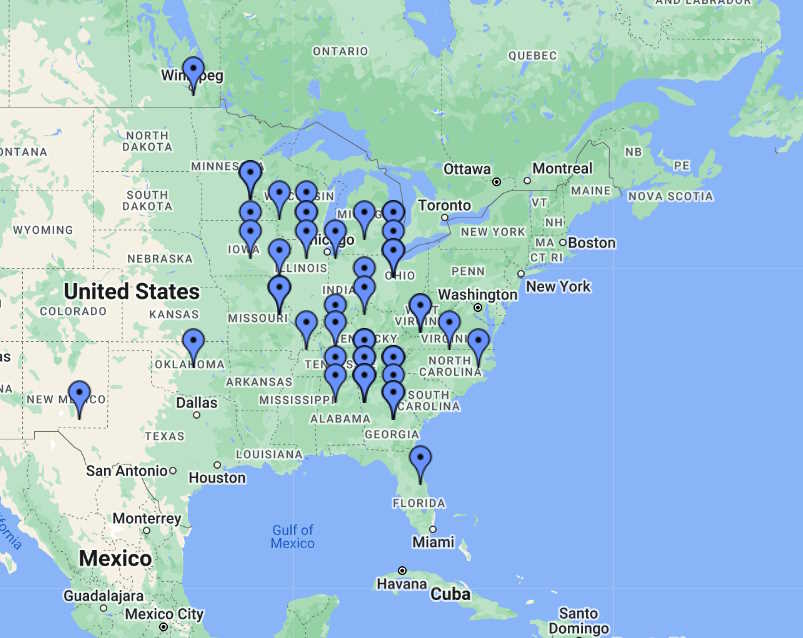
This is a quick plot of the contacts that I made during the activation (thank you, QSOMAPS.COM). Or so I thought, but then I counted. I had 66 contacts in the log. There are ~33 “balloons” on the map above. Each balloon, it turns out, represents a grid that I worked, not a call. The pattern also reflects that the antenna broadside was not exactly East-West, but about 10-ish degrees CCW from that. The spot that would have straightened the antenna out both vertically and directionally proved to have been paved and thus impenetrable with my tent stakes.